La méthode AMDEC : généralités.
- La méthode AMDEC a pour objectif d’accroitre la fiabilité des produits et des process.
- AMDEC signifie Analyse des Modes de Défaillance de leurs Effets et de leur Criticité.
- En anglais, l’acronyme est FMEA (Failure Mode and Effects Analysis).
- Il s‘agit d’une méthode d’analyse préventive utilisée en conception des produits et des process industriels mais qui peut également être utilisée pour les processus, en général.
- Très souvent assimilé (à tort) à un outil Qualité, l’AMDEC fait partie des techniques de Sureté de Fonctionnement (SdF : Fiabilité, Disponibilité, Maintenabilité, Sécurité et Testabilité).
- L’AMDEC peut être considéré comme un outil d’aide à la conception.
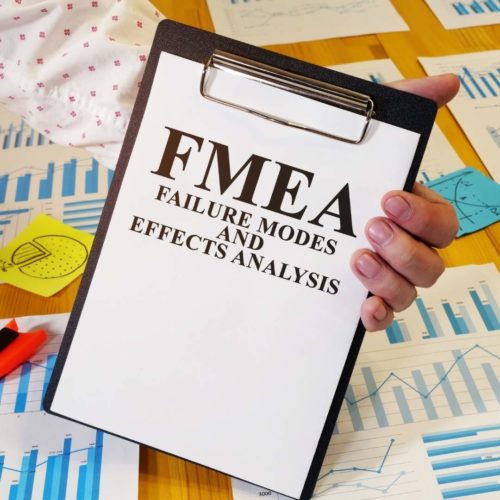
Demandez un devis pour la Formation
AMDEC Produit Process
Un bref historique
On relie bien souvent l’AMDEC avec la Loi de Murphy. Est-ce pour autant le capitaine du même nom qui est à l’origine de l’outil ? Le mystère demeure.
Pour mémoire ce scientifique de l’armée américaine est connu pour avoir été à l’origine d’une expérience restée célèbre : c’est lors d’un test de décélération et d’une erreur de câblage de son technicien (dont l’histoire n’a pas retenu le nom) que le Docteur Stapp (cobaye de l’expérience) a malencontreusement encaissé plus de 40 g.
If it can go wrong, it will (Si quelque chose peut mal tourner, alors ça tournera mal).
En résumé si un évènement critique a une faible probabilité d’apparition il est nécessaire d’y prêter un minimum d’attention. C’est cependant l’armée américaine qui semble avoir été à l’origine des première formes d’AMDEC. La méthode est ensuite utilisée par la NASA dans le cadre des premiers vols spatiaux habités pour être ensuite transférée dans l’industrie agro-alimentaire sous une variante toujours utilisée de nos jours (HACCP – Hazard Analysis and Critical Control Point).
C’est surtout dans les années 70 et notamment suite à l’affaire de la Ford Pinto (lien vers article Wikipédia) que l’AMDEC va connaitre son avènement. La généralisation de la méthode s’ensuit et ceci dans nombre de domaines (automobile, aéronautique, armement, pharmaceutique, ferroviaire, matériel médical, chimie, nucléaire, agro-alimentaire). Fin des années 2000 l’AMDEC Process inversé (Reverse-FMEA) apparait.
Objectif de la méthode AMDEC
L’objectif de la méthode AMDEC est de réduire les risques sur les produits et les process dès les premières phases de conception afin de réduire les risques sécurité (accidents…), règlementation et qualité (coûts de non-qualité).
Il s’agit d’augmenter la robustesse :
- Des produits: en guidant les choix de conception (choix des matériaux et des composants, dimensionnement, tolérances …), les validations (pertinences des tests et des essais) et la hiérarchisation des caractéristiques (caractéristiques spéciales).
- Des process : en mettant en place un Plan de Surveillance (Control Plan) pertinent avec notamment des Poka-Yoke ou de la Maitrise Statistique des Process (SPC/MSP). Le but de l’AMDEC Process n’est pas de mettre en place une batterie de contrôleurs en fin de ligne mais d’éviter que les défauts apparaissent.
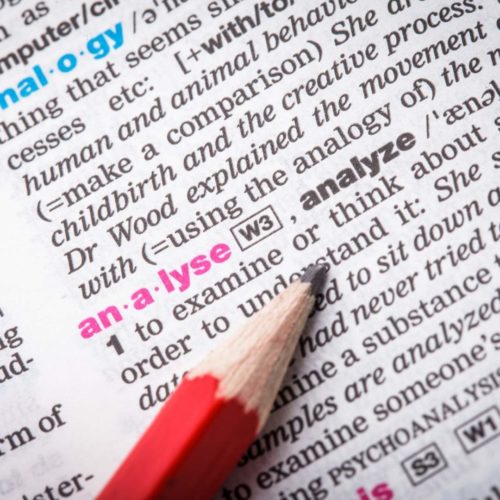
Vocabulaire
- Mode de défaillance: il s’agit de la forme observable d’un dysfonctionnement par l’un des 5 sens (ex: une fuite, une odeur anormale, un bruit, des traces de corrosion …), pour l’AMDEC process nous utiliserons Non-Conformité (ex: une vis manquante sur un produit en cours d’assemblage …).
- Effet : il s’agit de l’impact sur l’utilisateur (qui peut être le client). Ces conséquences peuvent affecter sa satisfaction mais également sa sécurité.
- Cause : Origines de la cause de la défaillance
- Gravité (G) : Estimation de l’impact de la défaillance sur l’utilisateur.
- Occurrence (O) : Probabilité que la défaillance se produise.
- Détection (D) : Probabilité que la défaillance soit détectée (on devrait plutôt non-détection car, nous le verrons plus tard la cotation fonctionne un peu à l’envers pour ce facteur).
- Criticité (C) : il s’agit de la multiplication des 3 facteurs on a donc : C = GxOxD
- Généralement G, O et D sont cotés de 1 à 10 selon des grilles qui sont propres à un secteur d’activité voir à une entreprise. A ce jour seul le secteur Automobile a réussi (en partie!) à construire un mode de cotation commun (AIAG-VDA).
Les étapes de la méthode AMDEC
- L’animateur
- Le chef de projet
- Des représentants des métiers (électronique, mécanique …)
- L’acheteur
- Un représentant des méthodes/engineering
- Un représentant de la Qualité
- Des experts (éventuellement les fournisseurs) pourront ponctuellement participer à des séances AMDEC.
2°) Planifier vos AMDEC.
Nous l’avons vu, les AMDEC (Produit et Process) doivent démarrer tôt dans le projet. Il est donc nécessaire de planifier des points AMDEC réguliers. Comptez au moins une dizaine de réunions pour un projet (même si tout dépend de sa taille). Ces revues doivent être limitées en temps (2/3 heures) car la charge mentale de ces rencontres est … importante.
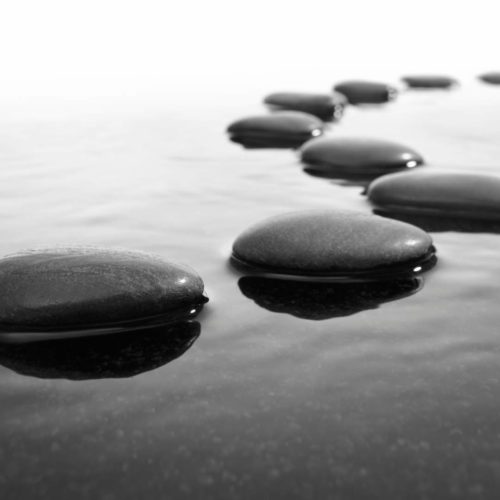
3°) Définir les limites de l’étude.
- AMDEC Produit : Quelles sont les limites du produit à concevoir : le couvercle de la cocotte-minute ou l’ensemble de la cocotte-minute ? À quel système appartient le produit : une pompe à injection haute pression fait partie d’un système injection.
- AMDEC Process : Quelles sont les opérations de production concernées ? Quels sont les flux amont et aval ?
4°) Rassembler les données d’entrée
AMDEC Produit
- Données marketing
- Plans
- Cahier des charges fonctionnel
- Liste des Caractéristiques Spéciales
- Spécifications (Techniques, réglementations et sécurité)
- Calculs et vérifications
- Programmes d’essais
- Résultats des essais déjà effectués ou en cours
- Les exigences commerciales pour la réparation, la maintenance
- Les conditions à respecter dans certains pays
- Historique qualité sur des produits similaires (Taux de panne, examen des retours, banques de données, non-conformités produits, 8D…)
- Objectifs Qualité (réclamations, retours garantie)
AMDEC Process
- Synoptique de production (Flow-chart)
- Cahier des Charges fonctionnel du process
- Liste de caractéristiques spéciales
- Formules, plans, spécification produit, spécification conditionnement
- 8D, arbres de défaillance, taux de rebuts, matrice de cause à effet
- Objectifs Qualité (Taux de rebuts, réclamations…)
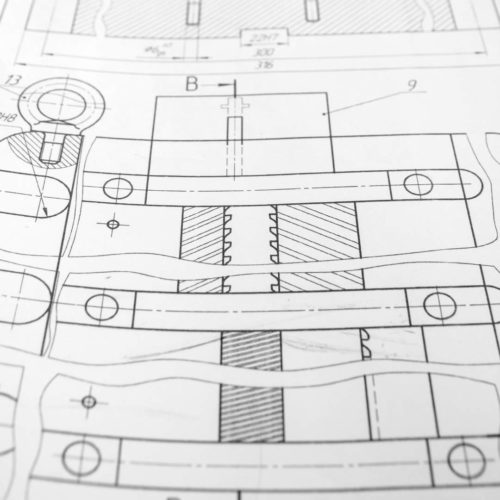
6°) Analyser et évaluer les défaillances potentielles
AMDEC Produit
- G : La gravité (effet de de la défaillance sur l’utilisateur)
- O : L’occurrence (probabilité d’apparition de la cause)
- D : La détection (probabilité de non détection) du mode et de la cause
AMDEC Process
Reprendre le synoptique de fabrication et déterminer pour chaque opération les non-conformités potentielles
- G : La gravité (effet de de la défaillance sur l’utilisateur). Attention l’utilisateur peut être: l’opérateur sur votre ligne de fabrication, l’opérateur de votre client direct ou le client final!
- O : L’occurrence (probabilité d’apparition de la cause)
- D : La détection (probabilité de non détection) de l’anomalie et de la cause.
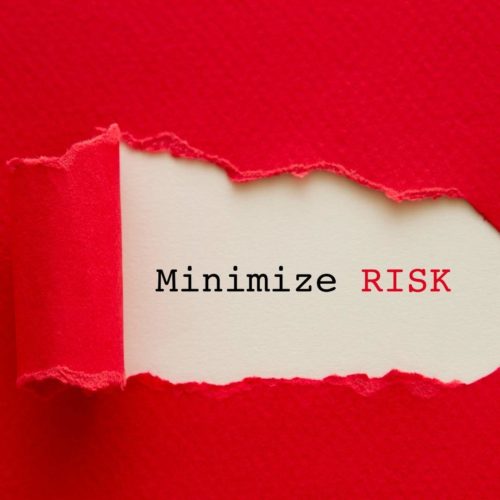
7°) Calculer la Criticité
Rappel C=GOD (facile à se rappeler et ça marche aussi à l’envers C=DOG). C est également parfois appeler IPR (Indice Prioritaire de Risque) ou RPN (Risk Priority Number).
8°) Mettre en place les Actions de Maitrise
Nous arrivons ensuite à un point délicat de l’AMDEC : la limite de C (La criticité) !
La croyance populaire tend à prétendre que si C < 100 on ne fait rien … on voit ainsi d’habiles C = 92 tranquillisants certes pour l’esprit, mais pas réellement satisfaisants … dans l’esprit de l’AMDEC.
En fait le calcul de C n’est réalisé que pour se donner des priorités et dans ce cas la limite 100 peut constituer une première étape.
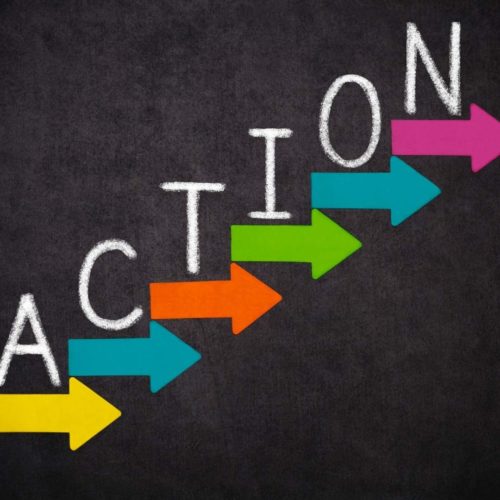
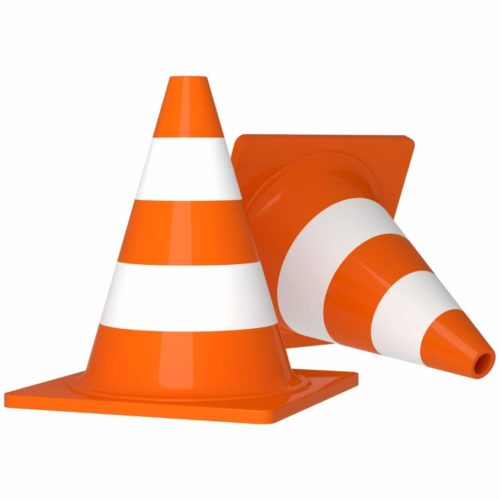
Quelques remarques sur la méthode AMDEC
- L’AMDEC est une méthode de travail de groupe (si c’est un ingénieur qualité qui fait son AMDEC dans un coin, c’est généralement mauvais signe)
- La définition de la limite de l’étude est essentielle
- En AMDEC Process adoptez un esprit LEAN : prévenez l’apparition (l’occurrence) des défauts (POKA YOKE, MSP, …) et considérez les contrôles (notamment en fin de ligne) comme des MUDA
- On mélange souvent Gravité et Occurrence : ce n’est pas parce qu’un caillou a moins de chance de vous tomber sur la tête (Occurrence) qu’il vous fera moins mal (Gravité) !
- En AMDEC Process on considère que les composants et matières premières des fournisseurs sont conformes. Ce postulat de base ne doit pas vous empêcher d’effectuer des contrôles par prélèvement à réception (surtout pendant la phase de démarrage). Par contre vous devez vous assurer que votre prestataire a également déployé la méthode AMDEC dans son organisation.
- Rappelez vous, lors de vos cotations que vos opérateurs sont compétents mais pas infaillibles (notamment dans le cadre des inspections visuelles).
- Conservez l’esprit KAIZEN : ne prenez en compte que les évidences et travaillez dans un esprit Amélioration Continue
- Le Retour d’Expérience est essentiel notamment pour déterminer l’occurrence. Vous devez avoir connaissance des incidents (Réclamations – Retours Garantie) sur les produits et process antérieurs ou similaires.
- Utilisez les outils de recherche des causes racines (5?, Ishikawa, Arbre de défaillance)
- Si vous modifiez votre process pensez à voir si cela a une influence sur votre AMDEC Process (c’est généralement le cas)
- Méfiez vous des AMDEC génériques
- Ne faites pas uniquement des AMDEC car le client la réclame
- Utilisez des grilles de cotation reconnues dans vos équipes, sinon vous aller passer des heures à parler de la grille
Découvrez notre formation sur AMDEC Produit Process